Sylatech uses 3D printing as part of their investment casting process. Before using Ultimaker 3D printers, customers had to directly invest in tooling needed for making their specific design in metal. However, if their metal part needs modifications, this can become a time consuming and costly addition to the process. Using an Ultimaker, the prototype can be finalized before investing in tooling for larger volume productions, cutting the risk of such changes.

Casting metal parts for prototyping from 3D prints
Sylatech is an investment casting firm that uses Ultimaker 3D printers to speed up their rapid prototyping process. Sylatech offers services in CNC machining, radio frequency and microwave manufacturing, and investment casting. They have been around for over 53 years and have customers in aerospace, space, defense, medical, automotive and construction.
Speeding up the prototyping process
With Ultimaker 3D printers, Sylatech can create a 3D printed model of the customer's design in a matter of days. These are then directly used to create a metal prototype. When modifications are needed to the design, the only additional cost is to 3D print the updated design.
The 3D printed part made from PLA already gives an accurate prototype before a single metal part is created. When the 3D print is accepted, the metal part can be created. By using the Ultimaker, design engineers can have a metal prototype of their design in just five days.
From 3D print to metal part
First, the 3D printed model is glued to a wax frame. When the whole part contains multiple objects, they can all be glued to the wax frame when size allows it. The wax frame is placed into a container which is then filled with a ceramic solution called slurry. When the container is placed in the oven, the slurry will harden, and the 3D printed PLA model is completely burnt out. This creates the mold where hot liquid metal is poured in.
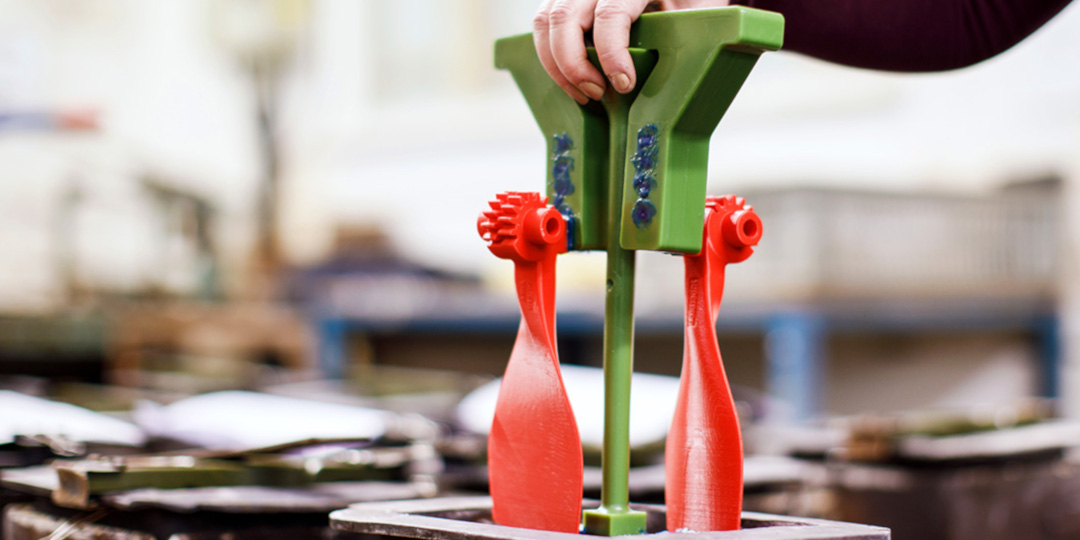
When the metal inside has cooled, the mold is broken away. The metal part is an exact duplicate of all the models inside and the original wax frame. Now, the models can be cut from the frame and smoothed by sanding. The metal part is now ready for testing.
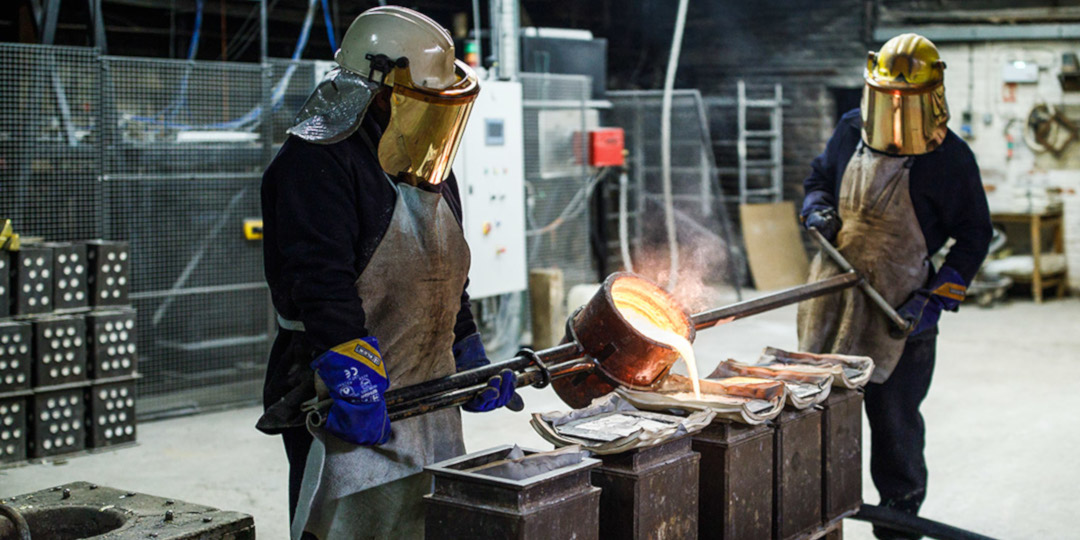
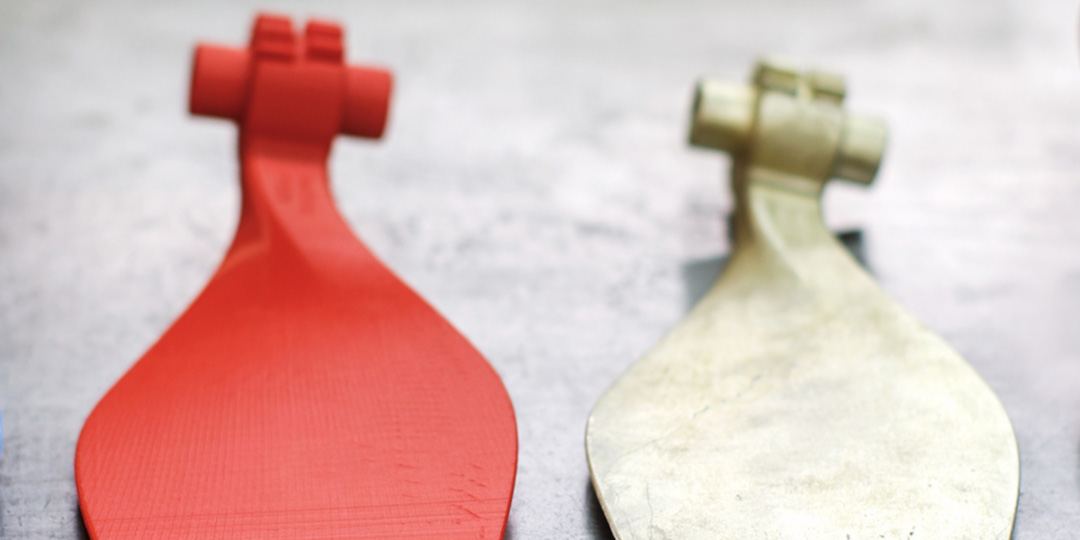
Saving on cost and extra development time
To create a model from wax, Sylatech has to create special tooling. Usually, a project which directly uses these tools will take five weeks to develop the first metal part. Adjusting the tooling when modifications are needed in the design costs roughly £500 per adjustment. However, when the Ultimaker is used, printing a new design costs only around £10 per part. Typically, 30% of designs need alterations after the first prototype. By using the Ultimaker to create the metal prototype, you minimize the chances of modifications to the tooling. So, this could not only save heaps of time but also on costs.
The use of 3D printing has clearly transformed the way we do business. And we will continue to use 3D printing and the Ultimaker to deliver benefits to our customers.
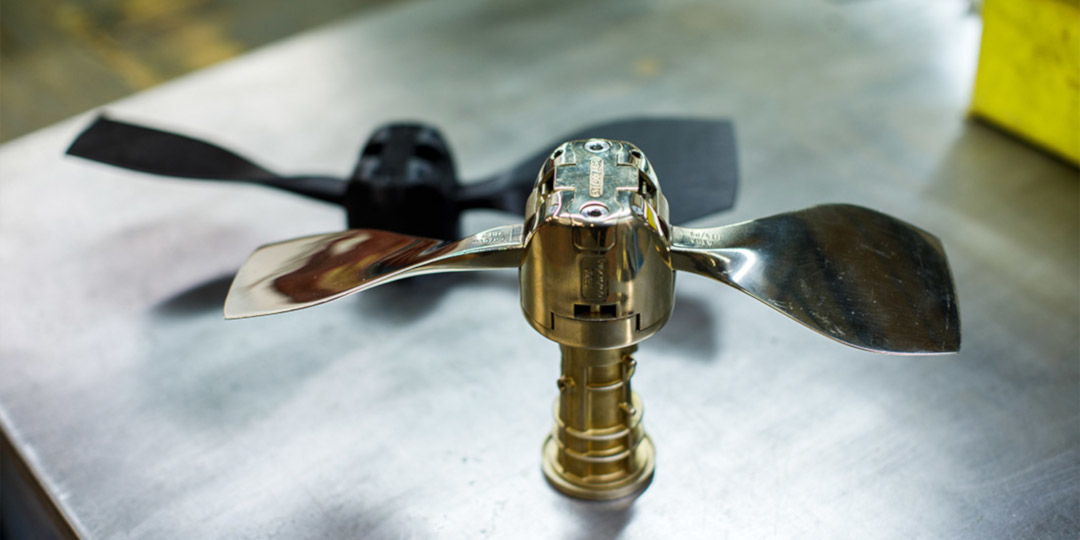
Using the Ultimaker within Sylatech
Sylatech started using 3D printers with the Ultimaker 2+. Using the printer gave great results right from the start. They drop the model on Ultimaker Cura’s build plate and almost instantly their design files are ready to become accurate 3D prints. After the success of using the Ultimaker 2+, Sylatech invested in the Ultimaker 3. The water-soluble PVA material enables Sylatech to print any design customers come up with.
Besides printing prototypes for customers, Sylatech also uses their 3D printers for various jigs, fixtures, and robotic components. They have a couple of robot-arms which automate a large part of their CNC process. Many parts of this robotic system are printed on their Ultimaker 3D printers.
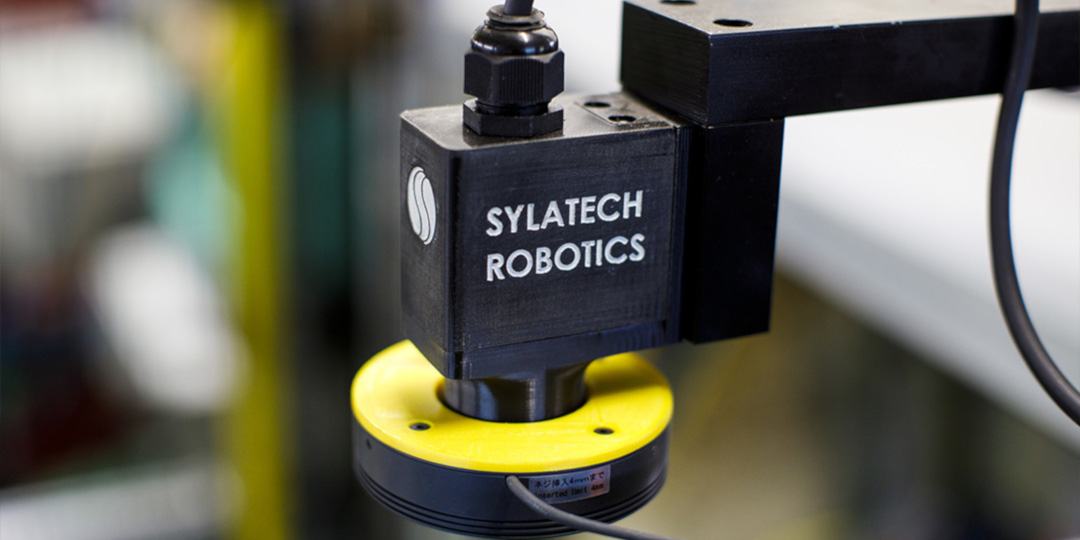

Sylatech is a great example of how adopting Ultimaker as a tool can bring benefits across a company. They have successfully optimized their investment-casting process and used 3D printers to help deliver other improvements to their workflow. But the best thing is that, through Sylatech’s application of Ultimaker technology, customers benefit directly from cost savings and receiving the final metal part their business needs faster than ever.